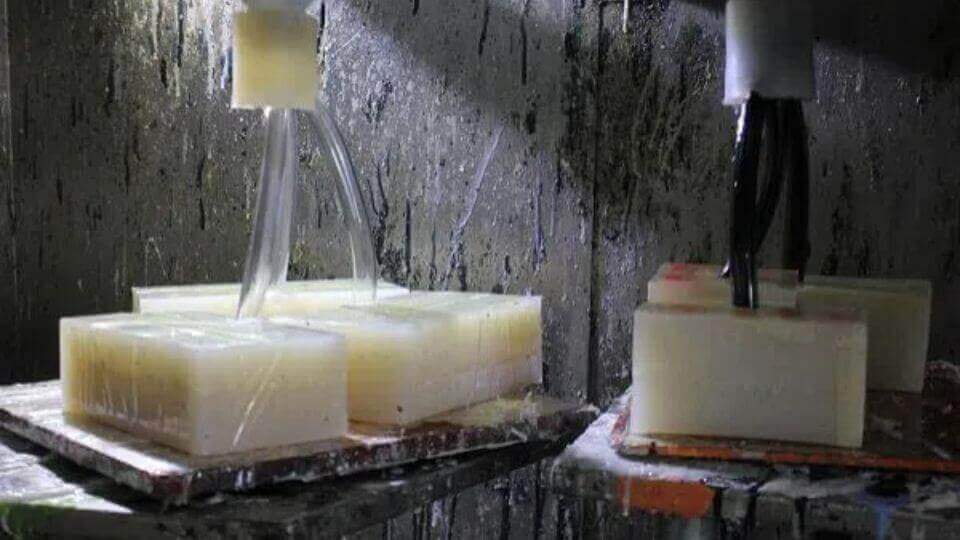
The wide variety of plastic materials available for injection molding can make selecting the right one challenging. From commonly used polymers to specialty plastics and polymer blends, there are hundreds of options, each with unique properties and processing needs. Additionally, various grades of the same plastic, including those with fillers like glass or carbon fibers, add to the complexity. Whether your project involves medical plastic injection molding, automotive components, or another application, PROTO MFG’s experts are equipped to guide you from design to production efficiently.
The Top 8 Plastic Injection Molding Materials
These are the most common plastic materials for injection molding:
-
acrylic (PMMA)
-
acrylonitrile butadiene styrene (ABS)
-
nylon (polyamide, PA)
-
polycarbonate (PC)
-
polyethylene (PE)
-
polyoxymethylene (POM)
-
polypropylene (PP)
-
polystyrene (PS)
Acrylic (PMMA)
Acrylic is a strong, transparent thermoplastic that is a lightweight, shatter-resistant alternative to glass. This injection molded material also has excellent optical clarity, allowing high light transmission. Resistant to ultraviolet (UV) light and weathering, acrylic is also known as PMMA or its full chemical name: polymethyl methacrylate.
Properties
Unlike some plastics, acrylics can withstand water attack and hold tight tolerances. PMMA does not absorb odors, but is not solvent resistant and easily stained by grease. While injection molded acrylics have high tensile strength, they are susceptible to stress cracking under heavy loads.
Applications
Applications for acrylic injection molding include windows, greenhouses, solar panels, bathroom enclosures, and other transparent parts for architectural, lighting, and outdoor applications.
Acrylonitrile Butadiene Styrene (ABS)
ABS has a relatively low melting point and is easy to mold. This opaque polymer can be used with colorants and a variety of textures and surface treatments. Its butadiene component provides excellent toughness even at low temperatures, while the styrene component provides a shiny, attractive surface finish on injection molded parts.
Properties
ABS is known for its strength and impact resistance, but lacks strong resistance to sunlight (UV), water, and weather. Compared to acrylics, injection molded ABS is not suitable for outdoor applications. Additionally, ABS produces a lot of smoke when burned and, unlike nylon, does not tolerate high friction very well.
Applications
ABS injection molding is used to produce many types of plastic parts, including:keyboard keys, protective headgear, electrical outlet wall plates, automotive parts like wheel covers, consumer goods.
Nylon Polyamide (PA)
Nylon is a synthetic polyamide (PA) that combines toughness and high heat resistance with high abrasion resistance, good fatigue resistance and noise reduction. Nylon itself is not flame retardant, but flame retardant versions are available. Similarly, although nylon is degraded by sunlight, UV stabilisers can be added to improve outdoor performance.
Properties
Compared to other plastics, nylon is less resistant to strong acids and bases. Nylon is not as strong as polypropylene and its impact resistance is not comparable to polycarbonate. Nylon injection moulding is challenging because it tends to shrink and is prone to underfilling of the mould.
Applications
Applications for nylon injection molding include strong mechanical parts such as bearings, bushings, gears, and slides.
Polycarbonate (PC)
Polycarbonate is strong, lightweight and naturally transparent. This plastic injection moulding material has excellent optical properties to support light transmission, yet retains its colour and strength when tinted. Although polycarbonate is not scratch resistant, it is much stronger than glass and very durable.
Properties
Injection moulded polycarbonate is sometimes used instead of acrylic because PC maintains its physical properties over a wider temperature range. However, PC requires higher processing temperatures, which can make moulding more expensive. However, because polycarbonate has predictable and uniform shrinkage, it provides precise dimensional control for tighter tolerances.
Applications
Applications for polycarbonate injection molding include machinery guards, clear molds for urethane and silicone casting.
Polyethylene (PE)
Polyethylene is the most commonly used plastic in the world and is a commercial polymer that can be selected based on density. Both High Density Polyethylene (HDPE) and Low Density Polyethylene (LDPE) are chemically resistant, but they differ in hardness, flexibility, melting point and optical clarity.
Properties
PE plastics include polyethylene terephthalate (PET, PETE), a material that is not defined by density. Like LDPE, PET can be as transparent as glass; however, designers can also choose grades of PET or PETE with different optical clarity.HDPE, LDPE, and PET are all moisture- and chemical-resistant, but LDPE is softer and more pliable than the opaque material HDPE.
Applications
Applications for polyethylene injection molding may be limited to indoor applications because of their poor UV resistance.
Polyoxymethylene (POM)
Polyoxymethylene (POM) is an engineering plastic also known as acetal. It combines excellent rigidity and thermal stability with a low coefficient of friction. This plastic material has low water absorption and good chemical resistance. In terms of appearance, POM plastic is naturally opaque and white in colour.
Properties
Pure acetal has low impact strength and very high thermal expansion. However, POM can be reinforced with glass fibres or minerals to increase strength and stiffness. Compounds reinforced with both materials provide an excellent balance of mechanical properties. Outdoor applications of injection moulded POM are limited by its lack of resistance to sunlight.
Applications
With its low coefficient of friction, injection-molded POM is used in bearings, gears, conveyor belts, and pulley wheels.
Polypropylene (PP)
Polypropylene is the second most commonly used plastic in the world. It has good chemical resistance, retains its shape after twisting or bending, has a high melting point and does not degrade in moisture or water. Injection-moulded polypropylene (sometimes called PP) can also be recycled.
Properties
Despite its comparative advantages, polypropylene degrades under UV light and is highly flammable. At temperatures above 212°F (100°C), this injection-moulded plastic dissolves into aromatic hydrocarbons, such as benzene and toluene, which are harmful to humans. Polypropylene plastics are also difficult to bond and paint.
Applications
Applications for polypropylene injection molding include toys, storage containers, sporting goods.
Polystyrene (PS)
Polystyrene plastics are lightweight, relatively inexpensive, and resistant to moisture and bacterial growth. These commercial plastics also have good chemical resistance to dilute acids and bases and excellent resistance to gamma radiation, which is used to sterilise medical devices.
Properties
There are two main types of polystyrene: General Purpose Polystyrene (GPPS) and High Impact Polystyrene (HIPS). GPPS is fragile and has lower dimensional stability than HIPS, which is blended with butadiene rubber to enhance its material properties. GPPS also has a glassy transparency, whereas HIPS is opaque.
Applications
Applications for polystyrene injection molding include medical, optical, electrical, and electronic applications.
Sourcing Simplified – Start Your Next Project With PROTO MFG
Are you looking for a reputable partner for your parts Injection molding projects? Look no further. At PROTO MFG, we specialize in CNC machining and related technologies, including sheet metal fabrication, rapid prototyping, etc. Whether it is a project with a simple design or parts with complex geometries, do not hesitate to contact us today!
Website of Source: https://www.mfgproto.com/
Source: Story.KISSPR.com
Release ID: 1103293