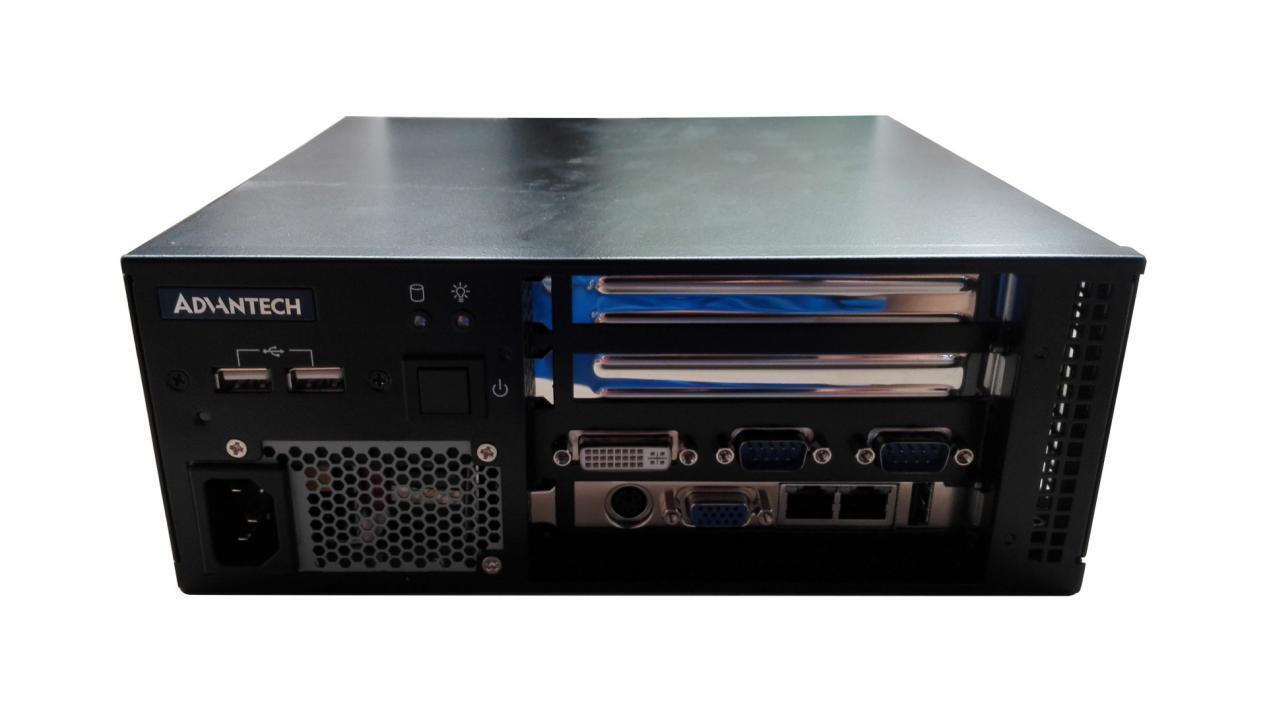
PLC (Programmable Logic Controller) and industrial computers (IPC) are both crucial devices in the field of industrial automation. Although they serve similar purposes, they have several differences in design, application, and functionality.
Characteristics of PLC:
-
Reliability: PLCs have a modular structure, making them highly reliable. Their mean time between failures (MTBF) is often in the tens of thousands of hours.
-
Adaptability: PLCs can adapt to various industrial environments. They are programmable to implement different control logics and meet diverse production requirements.
-
Ease of Programming: PLCs typically use user-friendly programming languages such as Ladder Logic and Function Block Diagram, making programming straightforward and fast.
-
Simple Maintenance: PLCs have a low failure rate, are easy to diagnose, and are relatively simple to maintain.
Characteristics of Industrial Computers (IPC):
-
Real-time Performance: IPCs have high real-time performance, enabling them to respond quickly to control system signals and provide precise control.
-
Stability: IPCs use industrial-grade motherboards and processors, ensuring high stability and reliability.
-
Expandability: IPCs offer rich interfaces and expansion slots, allowing them to connect to a variety of external devices and support complex control functions.
-
Simple Maintenance: Like PLCs, IPCs also have a low failure rate and are relatively easy to maintain.
Key Differences Between PLC and IPC:
Application Scope:
-
PLCs are suited for simpler industrial control tasks such as controlling switches or analog inputs/outputs in production lines.
-
IPCs are used for more complex control tasks, such as large-scale control systems or data acquisition systems.
Programming Method:
-
PLCs use simplified, intuitive programming languages like Ladder Logic, making them easier for operators and engineers to program.
-
IPCs typically require professional programming knowledge, often using languages such as C, C++, or specialized industrial control software.
Real-time Requirements:
-
IPCs typically have higher real-time requirements and need to quickly process and respond to control signals.
-
PLCs have lower real-time demands but still need to provide reliable and fast response times within industrial environments.
Expandability:
-
IPCs offer better expandability due to their multiple interface options and expansion slots, making them suitable for more complex systems and peripheral connections.
-
PLCs are more limited in terms of expandability but can still use additional modules to extend functionality.
Maintenance Difficulty:
-
PLCs are easier to maintain, with less complex diagnostics and a lower failure rate.
-
IPCs can be more challenging to maintain, requiring more advanced troubleshooting and technical expertise.
Development Trends:
As industrial automation continues to evolve, both PLCs and IPCs are becoming smarter, more networked, precise, and multifunctional. The development of the Internet of Things (IoT) is also influencing these devices, pushing them toward greater integration with IoT technologies for smarter, more automated industrial control solutions.
In conclusion, both PLCs and IPCs are indispensable in industrial automation. While they differ in certain aspects, they each play a vital role in meeting the diverse needs of industrial control. As technology advances, both devices will continue to innovate, providing more opportunities and challenges for the automation industry.
PLCs are simpler, more reliable for straightforward tasks, and are easier to program and maintain, making them ideal for basic industrial automation.
IPCs, on the other hand, are suited for complex, large-scale systems requiring high computational power, rapid responses, and expandability.
Both have essential roles in industrial automation, but the choice between them depends on the complexity of the task at hand.
Website of Source: https://iainventory.com/
Source: Story.KISSPR.com
Release ID: 1288333